Are you curious about the giants of the electrical world? Let's dive into the fascinating realm of tank transformers!
Tank transformers are large, oil-filled electrical devices that change voltage levels in power systems. They're crucial for efficient power transmission and distribution, using electromagnetic induction to step voltage up or down as needed.
I've spent years working with these behemoths, and I'm excited to share my knowledge with you. From their basic principles to cutting-edge innovations, we'll explore every aspect of tank transformers. Ready to power up your understanding? Let's get started!
What Is a Tank Transformer: The Powerhouse Behind Industrial Electricity?
Have you ever wondered what those massive metal containers at electrical substations are? They're the unsung heroes of our power grid!
A tank transformer is a large, oil-filled electrical transformer used in power systems to change voltage levels. It's essential for efficient power transmission and distribution, capable of handling high voltages and large loads.
In my years working with these giants, I've come to appreciate their crucial role in our electrical infrastructure. Let me break it down for you:
Key Features of Tank Transformers
- Size: They're much larger than distribution transformers, often weighing several tons.
- Oil-Filled: They use oil for insulation and cooling.
- High Capacity: They can handle voltages from thousands to millions of volts.
- Efficiency: They're designed for minimal energy loss during voltage transformation.
- Durability: Built to last decades with proper maintenance.
Let's look at some typical specifications:
Feature | Typical Range |
---|---|
Power Rating | 5 MVA to 1000 MVA |
Primary Voltage | 33 kV to 765 kV |
Secondary Voltage | 11 kV to 400 kV |
Efficiency | 98% to 99.75% |
Lifespan | 25 to 40 years |
I remember my first encounter with a tank transformer during a substation tour. The sheer size and complexity left me in awe. It was then that I realized the immense engineering that goes into powering our world.
Why Tank Transformers Matter
- Power Transmission: They enable long-distance power transmission by stepping up voltage.
- Industrial Use: They provide the right voltage levels for large industrial operations.
- Grid Stability: They help maintain voltage levels across the power grid.
- Energy Efficiency: By reducing transmission losses, they make our power system more efficient.
Understanding tank transformers is crucial for anyone involved in power systems. They're the backbone of our electrical infrastructure, silently working to ensure we have the power we need, when and where we need it.
Core Principles of Tank Transformers: Electromagnetic Induction Explained?
Ever wondered how these massive machines actually work? It all comes down to a principle discovered nearly 200 years ago!
Tank transformers operate on the principle of electromagnetic induction. They use changing magnetic fields to transfer electrical energy between circuits, allowing for voltage transformation without direct electrical connection.
I've spent countless hours studying and working with these principles. Let me break it down in a way that I wish someone had explained to me when I was starting out:
The Basics of Electromagnetic Induction
- Faraday's Law: A changing magnetic field induces a voltage in a nearby conductor.
- Primary Coil: Creates a changing magnetic field when alternating current flows through it.
- Magnetic Core: Concentrates and directs the magnetic field.
- Secondary Coil: The changing magnetic field induces a voltage in this coil.
- Turns Ratio: The ratio of turns in the primary and secondary coils determines the voltage change.
Let's look at the key components and their roles:
Component | Function |
---|---|
Primary Coil | Receives input voltage |
Secondary Coil | Produces output voltage |
Magnetic Core | Directs magnetic flux |
Insulating Oil | Provides insulation and cooling |
I remember teaching this concept to a group of interns. To demonstrate, I used a simple hand-wound transformer. Seeing their faces light up when they grasped how changing the number of turns affected the output voltage was a highlight of my career.
Diving Deeper into the Physics
- Magnetic Flux: The total magnetic field passing through a given area.
- Mutual Inductance: How changes in current in one coil affect voltage in another.
- Eddy Currents: Circulating currents in the core that cause energy loss.
- Hysteresis: The lag in magnetization of the core material.
These principles aren't just theoretical. They directly impact transformer design and efficiency. For instance, we use laminated cores to reduce eddy currents and choose core materials carefully to minimize hysteresis losses.
Practical Applications
- Voltage Step-Up: For long-distance power transmission, we increase voltage to reduce current and minimize losses.
- Voltage Step-Down: Near points of use, we decrease voltage for safe distribution to homes and businesses.
- Isolation: Transformers provide electrical isolation between circuits, enhancing safety.
- Phase Shifting: Some specialized transformers can shift the phase of voltages, useful for power flow control.
Understanding these core principles is crucial for anyone working with or designing transformers. It's not just about memorizing formulas; it's about grasping how these fundamental laws of physics shape our entire power distribution system.
Anatomy of a Tank Transformer: Key Components and Their Functions?
Have you ever wondered what's inside those massive tanks? Let's take a virtual tour of a tank transformer's internals!
A tank transformer consists of several key components: the core, windings, insulating oil, bushings, and cooling system. Each part plays a crucial role in the transformer's operation, efficiency, and safety.
In my years of working with these machines, I've had the opportunity to see inside many transformers. It's always fascinating, and I'm excited to share this knowledge with you:
Key Components of a Tank Transformer
- Core: The heart of the transformer, usually made of laminated silicon steel.
- Windings: Primary and secondary coils, typically made of copper or aluminum.
- Insulating Oil: Provides insulation and cooling.
- Bushings: Connect the internal windings to external circuits.
- Tank: Houses all the components and contains the insulating oil.
- Cooling System: Radiators and fans to dissipate heat.
- Tap Changer: Adjusts the turns ratio to regulate output voltage.
Let's break down these components and their functions:
Component | Function | Material |
---|---|---|
Core | Directs magnetic flux | Silicon steel |
Windings | Carry current | Copper or aluminum |
Insulating Oil | Insulates and cools | Mineral oil or synthetic alternatives |
Bushings | Connect to external circuits | Porcelain or polymer |
Tank | Contains and protects | Steel |
Cooling System | Dissipates heat | Steel radiators, fans |
Tap Changer | Regulates voltage | Mechanical or electronic switches |
I once had the opportunity to oversee the assembly of a large power transformer. Watching each component come together was like seeing a complex puzzle being solved. It gave me a deep appreciation for the engineering involved.
Diving Deeper into Component Functions
-
Core Design:
- Laminated to reduce eddy currents
- Shape (core-type or shell-type) affects efficiency and size
-
Winding Configurations:
- Disc, helical, or layer windings
- Affects short-circuit strength and cooling efficiency
-
Insulating Oil:
- Acts as a dielectric
- Transfers heat from windings to cooling system
- Provides information about transformer health through oil analysis
-
Bushings:
- Designed to withstand high voltages and mechanical stresses
- Often oil-filled or resin-impregnated
-
Cooling Systems:
- ONAN (Oil Natural Air Natural)
- ONAF (Oil Natural Air Forced)
- OFAF (Oil Forced Air Forced)
- ODAF (Oil Directed Air Forced)
-
Tap Changers:
- On-Load Tap Changers (OLTC) for voltage regulation under load
- De-energized Tap Changers (DETC) for occasional adjustments
Understanding these components and their interactions is crucial for transformer design, maintenance, and troubleshooting. Each part plays a vital role in the transformer's performance, efficiency, and lifespan.
In my experience, a thorough understanding of these components can make all the difference in diagnosing issues and optimizing performance. It's not just about knowing what each part does, but how they work together as a system.
The Role of Oil in Tank Transformers: Insulation, Cooling, and Protection?
Ever wondered why transformers are filled with oil? It's not just to make them heavier!
Insulating oil in tank transformers serves three critical functions: electrical insulation, cooling, and protection against moisture and contaminants. It's a key component that significantly impacts the transformer's performance and lifespan.
Throughout my career, I've seen firsthand how crucial transformer oil is. Let me share some insights:
The Triple Role of Transformer Oil
-
Electrical Insulation:
- High dielectric strength
- Prevents arcing between components
-
Cooling:
- Absorbs heat from windings and core
- Circulates to dissipate heat
-
Protection:
- Prevents moisture ingress
- Slows down paper insulation degradation
Let's look at some key properties of transformer oil:
Property | Function | Typical Value |
---|---|---|
Dielectric Strength | Insulation | >30 kV/2.5mm |
Viscosity | Heat Transfer | 8-12 cSt at 40°C |
Flash Point | Safety | >140°C |
Moisture Content | Insulation Quality | <20 ppm |
Acidity | Oil Degradation Indicator | <0.03 mg KOH/g |
I remember a case where a transformer failed prematurely. Upon investigation, we found that the oil had degraded due to moisture ingress. It was a stark reminder of how critical oil quality is to transformer health.
Diving Deeper into Oil Functions
-
Insulation Properties:
- Oil fills gaps between windings and other components
- Its high dielectric strength prevents electrical breakdown
- Works in conjunction with cellulose insulation (paper and pressboard)
-
Cooling Mechanism:
- Natural convection in smaller transformers
- Forced circulation in larger units
- Oil's heat capacity and thermal conductivity are crucial
-
Protective Aspects:
- Acts as a barrier against moisture
- Dissolves gases produced by electrical and thermal stress
- Oil analysis can provide early warning of transformer problems
Oil Maintenance and Monitoring
-
Regular Testing:
- Dielectric strength
- Acidity
- Moisture content
- Dissolved gas analysis (DGA)
-
Oil Treatment:
- Filtration to remove particles
- Degassing to remove dissolved gases
- Dehydration to remove moisture
-
Oil Replacement:
- Partial or complete oil change when severely degraded
- Use of oil regeneration systems in some large transformers
Understanding and maintaining oil quality is crucial for transformer longevity. In my experience, a well-maintained oil system can significantly extend a transformer's life and improve its reliability.
The role of oil in tank transformers is a perfect example of how a single component can serve multiple critical functions. It's not just a filler; it's an active part of the transformer's operation, constantly working to keep the transformer running efficiently and safely.
Types of Tank Transformers: Choosing the Right One for Your Application?
Confused by the variety of tank transformers out there? Let's demystify the options!
Tank transformers come in various types, each designed for specific applications. The main categories include step-up, step-down, distribution, power, and special-purpose transformers. Choosing the right type is crucial for system efficiency and reliability.
In my years of consulting on transformer projects, I've helped many clients navigate this decision. Here's what you need to know:
Main Types of Tank Transformers
-
Step-Up Transformers:
- Increase voltage for long-distance transmission
- Used at power generation plants
-
Step-Down Transformers:
- Decrease voltage for distribution
- Found at substations near points of use
-
Distribution Transformers:
- Supply final voltage transformation for end-users
- Commonly seen in residential areas
-
Power Transformers:
- Handle high voltages and large loads
- Used in transmission substations
-
Special-Purpose Transformers:
- Includes rectifier transformers, furnace transformers, etc.
- Designed for specific industrial applications
Let's compare some key features:
Type | Typical Voltage Range | Common Applications |
---|---|---|
Step-Up | 11kV to 765kV | Power Generation |
Step-Down | 765kV to 33kV | Transmission Substations |
Distribution | 33kV to 415V | Residential/Commercial Supply |
Power | 33kV to 765kV | Industrial Facilities |
Special-Purpose | Varies | Specific Industrial Processes |
I once worked on a project where the client initially wanted a standard power transformer for their new factory. After analyzing their specific needs, we realized a special-purpose rectifier transformer would be more efficient. It's a perfect example of why understanding these types is so important.
Factors to Consider When Choosing a Transformer
-
Voltage Requirements:
- Input and output voltage levels
- Voltage regulation needs
-
Power Rating:
- Current load requirements
- Future expansion plans
-
Environmental Conditions:
- Indoor or outdoor installation
- Temperature extremes
- Altitude
-
Efficiency:
- Energy loss considerations
- Cost of operation over time
-
Special Features:
- Tap changing capabilities
- Cooling system requirements
- Noise level restrictions
-
Maintenance and Lifespan:
- Expected operational life
- Maintenance requirements and accessibility
-
Cost:
- Initial investment
- Total cost of ownership
Choosing the right transformer is not just about matching voltage and power ratings. It's about understanding the specific needs of your application and the environment in which the transformer will operate.
In my experience, taking the time to thoroughly assess these factors can lead to significant long-term benefits in terms of efficiency, reliability, and cost-effectiveness. It's not uncommon for the right choice to pay for itself many times over during the transformer's lifespan.
Remember, the best transformer for your application is one that not only meets your current needs but also accommodates future growth and changes in your power system. Don't hesitate to consult with experts who can help you navigate this complex decision.
Efficiency and Losses in Tank Transformers: How to Optimize Performance?
Worried about energy waste in your transformer? You're not alone. Let's tackle this crucial issue!
Efficiency in tank transformers is about minimizing energy losses. The main types of losses are core (no-load) losses and copper (load) losses. Optimizing these can significantly improve transformer performance and reduce operating costs.
%[Diagram of transformer
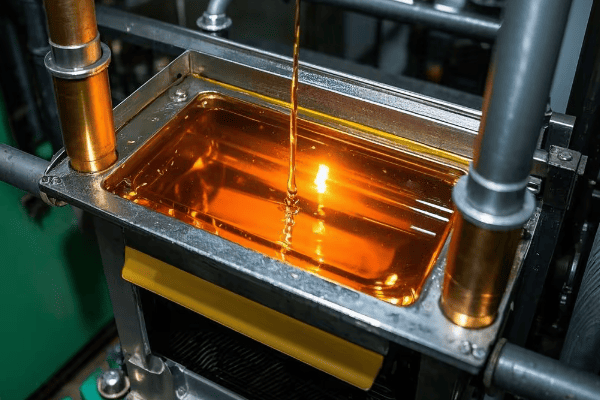
Throughout my career, I've been obsessed with squeezing every bit of efficiency out of transformers. Here's what I've learned:
Understanding Transformer Losses
-
Core Losses (No-Load Losses):
- Occur in the magnetic core
- Present even when the transformer is energized but not supplying load
- Mainly due to hysteresis and eddy currents
-
Copper Losses (Load Losses):
- Occur in the windings
- Increase with the square of the load current
- Caused by resistance in the conductor
Let's break down these losses:
Loss Type | Cause | How to Reduce |
---|---|---|
Hysteresis Loss | Magnetic domain alignment | Use low-loss core materials |
Eddy Current Loss | Circulating currents in core | Use laminated core design |
I²R Loss | Current flowing through winding resistance | Use larger conductors, reduce current density |
Stray Loss | Leakage flux in structural parts | Optimize design, use magnetic shielding |
I once worked on a project where we reduced a transformer's losses by 15% simply by upgrading the core material and optimizing the winding design. The energy savings over the transformer's lifetime more than justified the initial investment.
Strategies to Improve Efficiency
-
Core Material Selection:
- Use high-grade silicon steel or amorphous metals
- Consider grain-oriented steel for better performance
-
Core Design:
- Optimize lamination thickness
- Use step-lap joints to reduce flux leakage
-
Winding Design:
- Use larger conductor cross-sections to reduce resistance
- Optimize current density in windings
-
Cooling System Efficiency:
- Ensure proper oil circulation
- Use efficient radiator designs
-
Load Management:
- Operate transformers near their optimal load point
- Use parallel operation for better load distribution
-
Regular Maintenance:
- Keep oil clean and dry
- Monitor and maintain proper oil levels
-
Temperature Control:
- Maintain optimal operating temperature
- Use efficient cooling methods (ONAN, ONAF, OFAF, ODAF)
Improving efficiency is not just about reducing energy waste; it's about extending the transformer's life and reducing operational costs. In my experience, even small improvements in efficiency can lead to significant savings over time, especially for large power transformers.
The Impact of Efficiency on Total Cost of Ownership
- Energy Savings: Higher efficiency means lower energy bills over the transformer's lifetime.
- Reduced Cooling Requirements: More efficient transformers generate less heat, potentially reducing cooling system costs.
- Extended Lifespan: Lower losses mean less stress on insulation, potentially extending the transformer's life.
- Environmental Impact: Improved efficiency reduces carbon footprint, an increasingly important consideration.
Remember, when evaluating transformer efficiency, it's crucial to consider the total cost of ownership, not just the initial purchase price. A more efficient transformer might cost more upfront but can save significantly over its operational life.
In my years of working with transformers, I've seen the focus shift increasingly towards efficiency. It's not just about meeting minimum standards anymore; it's about pushing the boundaries of what's possible in transformer design and operation.
Tank Transformer Cooling Systems: ONAN, ONAF, OFAF, and ODAF Explained?
Ever wondered how these massive transformers keep their cool? Let's dive into the world of transformer cooling!
Tank transformer cooling systems are crucial for maintaining optimal operating temperatures. The main types are ONAN (Oil Natural Air Natural), ONAF (Oil Natural Air Forced), OFAF (Oil Forced Air Forced), and ODAF (Oil Directed Air Forced), each offering different cooling capacities.
I've worked with all these cooling systems, and each has its place. Let me break them down for you:
Types of Cooling Systems
-
ONAN (Oil Natural Air Natural):
- Simplest and most common for smaller transformers
- Relies on natural convection of oil and air
-
ONAF (Oil Natural Air Forced):
- Uses fans to increase air flow over radiators
- Suitable for medium-sized transformers
-
OFAF (Oil Forced Air Forced):
- Uses pumps to circulate oil and fans for air cooling
- Used in larger transformers
-
ODAF (Oil Directed Air Forced):
- Similar to OFAF, but with directed oil flow through windings
- Most efficient for very large transformers
Let's compare these systems:
Cooling Type | Oil Circulation | Air Cooling | Typical Application |
---|---|---|---|
ONAN | Natural | Natural | Small transformers |
ONAF | Natural | Forced | Medium transformers |
OFAF | Forced | Forced | Large transformers |
ODAF | Directed Forced | Forced | Very large transformers |
I remember upgrading a transformer from ONAN to ONAF cooling. The improvement in cooling efficiency allowed the transformer to handle higher loads without overheating, effectively extending its useful capacity.
Diving Deeper into Cooling Systems
-
ONAN Cooling:
- Relies on temperature difference for oil circulation
- Simple and reliable, but limited cooling capacity
- Suitable for transformers up to about 5 MVA
-
ONAF Cooling:
- Adds fans to increase air flow over radiators
- Can increase cooling capacity by 20-30% over ONAN
- Fans typically controlled by winding temperature
-
OFAF Cooling:
- Uses pumps to force oil circulation
- Significantly increases cooling efficiency
- Allows for more compact transformer design
-
ODAF Cooling:
- Directs oil flow through specially designed ducts in windings
- Provides most efficient cooling for hot spots
- Used in transformers over 100 MVA
Factors Influencing Cooling System Selection
- Transformer Size and Rating: Larger transformers generally require more advanced cooling.
- Environmental Conditions: Ambient temperature and altitude affect cooling efficiency.
- Load Profile: Transformers with high or fluctuating loads may need more robust cooling.
- Noise Restrictions: Forced air systems can be noisier, which may be a concern in some locations.
- Maintenance Requirements: More complex systems generally require more maintenance.
- Cost Considerations: More advanced cooling systems increase initial and operational costs.
In my experience, choosing the right cooling system is crucial for transformer performance and longevity. It's not just about handling the current load; it's about planning for future needs and ensuring the transformer can operate efficiently under various conditions.
I've seen cases where inadequate cooling led to premature transformer failure, and others where over-specifying the cooling system led to unnecessary costs. The key is to balance current needs, future growth, and operational efficiency.
Remember, a well-designed cooling system not only protects the transformer from overheating but can also extend its lifespan and improve its overall efficiency. It's an investment in the long-term health of your power system.
Safety Features in Tank Transformers: Protecting Against Electrical Faults?
Worried about transformer safety? You should be! Let's explore how these giants stay safe.
Tank transformers incorporate various safety features to protect against electrical faults, overloading, and other hazards. These include circuit breakers, pressure relief devices, Buchholz relays, and temperature monitors, all working together to ensure safe operation.
In my years working with transformers, I've seen how crucial these safety features are. Here's what you need to know:
Key Safety Features in Tank Transformers
-
Circuit Breakers:
- Interrupt current flow during faults
- Protect transformer from overloads
-
Pressure Relief Devices:
- Release pressure buildup in the tank
- Prevent explosion in case of internal faults
-
Buchholz Relay:
- Detects gas accumulation and oil flow changes
- Provides early warning of internal faults
-
Temperature Monitors:
- Track oil and winding temperatures
- Trigger alarms or shutdowns if temperatures exceed safe limits
-
Differential Protection:
- Compares current entering and leaving the transformer
- Detects internal faults quickly
Let's break down these features:
Safety Feature | Function | Action Taken |
---|---|---|
Circuit Breaker | Overcurrent protection | Interrupts power |
Pressure Relief | Overpressure protection | Releases pressure |
Buchholz Relay | Gas/oil flow detection | Alarms or trips |
Temperature Monitor | Overheating protection | Alarms or trips |
Differential Relay | Internal fault detection | Trips transformer |
I once witnessed a Buchholz relay save a large power transformer from catastrophic failure. It detected a small internal fault before it could escalate, allowing for a controlled shutdown and repair.
Diving Deeper into Safety Systems
-
Overcurrent Protection:
- Primary and backup protection schemes
- Coordination with other system protections
-
Overvoltage Protection:
- Surge arresters to handle lightning and switching surges
- Tap changers for voltage regulation
-
Cooling System Safeguards:
- Monitors for oil levels and flow
- Backup cooling systems in critical applications
-
Fire Protection:
- Fire-resistant oils or dry-type designs for indoor use
- Fire suppression systems in transformer vaults
-
Environmental Protection:
- Oil containment systems to prevent spills
- Noise reduction measures
-
Monitoring and Diagnostics:
- Online monitoring systems for real-time data
- Dissolved gas analysis (DGA) for early fault detection
In my experience, a comprehensive safety system is not just about preventing catastrophic failures. It's about early detection, controlled responses, and minimizing downtime. I've seen cases where advanced monitoring systems detected developing faults weeks before they would have caused problems, allowing for planned maintenance instead of emergency repairs.
The Importance of Regular Testing and Maintenance
- Routine Testing: Regular tests of protection systems ensure they'll work when needed.
- Calibration: Sensors and relays need periodic calibration to remain accurate.
- Upgrades: Safety systems should be updated as technology improves.
- Training: Operators need to understand and respond to safety system alerts.
Safety in transformer operation is not just about having the right features; it's about maintaining them, understanding them, and responding appropriately when they activate. In my years in the field, I've learned that a culture of safety awareness is just as important as the technical safeguards.
Remember, while these safety features are crucial, they're not a substitute for proper design, operation, and maintenance. They're the last line of defense in a comprehensive approach to transformer safety.
Conclusion
Tank transformers are the unsung heroes of our electrical grid, silently working to ensure power flows efficiently from generation to end-use. From their basic principles to advanced safety features, these complex machines are marvels of engineering.
We've explored their anatomy, the crucial role of insulating oil, various types and cooling systems, efficiency considerations, and vital safety features. Each aspect plays a critical role in the reliable operation of our power systems.
As technology advances, so do transformers, becoming more efficient, safer, and smarter. Understanding these devices is key to maintaining and improving our electrical infrastructure. Whether you're an engineer, a student, or just curious, I hope this guide has illuminated the fascinating world of tank transformers.
🚀Next steps, you can:
A. Learn about smart grid integration with transformers
B. Explore transformer maintenance and diagnostics
C. Investigate emerging transformer technologies
D. Study the environmental impact of transformer oils
E. Discover career opportunities in power systems engineering
F. Delve into the economics of transformer efficiency